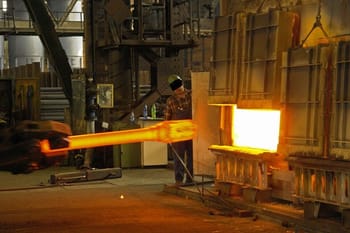
Offshore sourcing for custom steel forgings manufactured to meet your requirements.
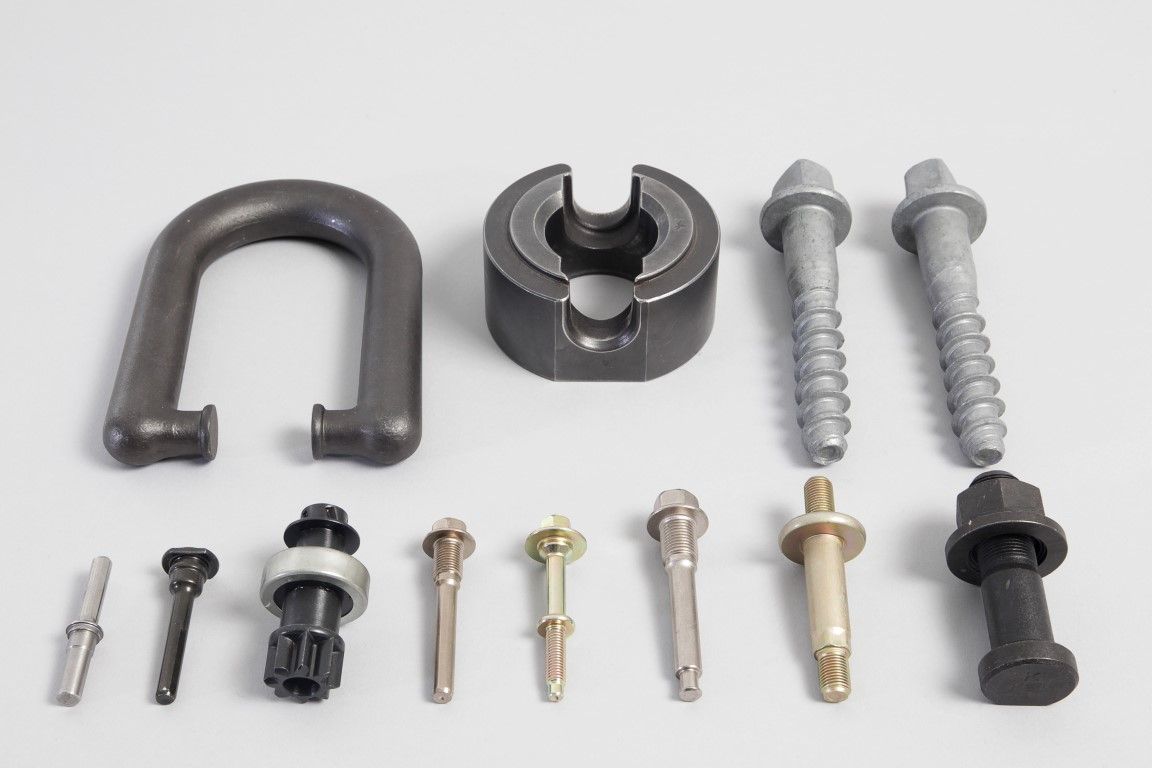
Forging parts
Offshore Sourcing for Steel Forgings
The forged steel manufacturing process involves the shaping of metal using localized compressive forces. The blows are delivered with a hammer (power hammer) or a die. Steel forgings are often classified according to the temperature at which it is performed: cold forging, warm forging, or hot forging. For the latter two, the metal is heated, usually in a forge. Forged parts can range in weight from less than a kilogram to hundreds of metric tons.
Offshore Steel Forging Suppliers
If your needs require you to produce either small or complex components or a combination of both, our offshore manufacturering partners in southeast Asia deliver products that match your specifications, with fast turnarounds at a fraction of the cost of domestic manufacturing. All our offshore manufacturers have been fully vetted, have years of experience and are highly skilled in their respective manufacturing fields.
Contact Sun Fast today for more information on how our offshore outsourcing for forged steel components can improve your business's efficiency, supply chain and bottom line. View our step by step offshore manufacturing process and then request a quote for in-depth price analysis.
Custom Metal Forgings
Depending on the demands of your part designs, products can be hot forged or cold headed. Hot forging is ideal for larger parts and applications where optimum yield strength, high ductility, and better surface quality are preferred. Cold heading is better suited to producing smaller parts and components, and the process automatically work-hardens the material, resulting in high strength products.
Cold Heading & Hot Forging
Our valuable offshore partners provide both hot forging and cold heading to meet the forged steel requirements of nearly any industry or application. As needed, we will work with you to determine the best forging method for your unique project.
Hot Forging
The hot forging of forged steel is the preferred method for creating parts and components for more rugged applications, such as construction and automotive manufacturing. The hot forging process improves the yield strength, ductility, and toughness of the material, making for more durable parts. Our offshore forging sources can hot forge a wide range of metals and alloys. For improved pricing and timely shipments, consider offshore outsourcing for forged steel to improve the way your business operates.
Cold Heading
Cold heading is ideal for producing smaller, more intricate parts and components, like those found in medical devices or electronics. Cold heading utilizes high speed, automated equipment to create perfectly repeatable, high precision parts. Our offshore manufacturers can cold head forge numerous metals and specialty alloys.
Steel Forging Benefits
The forging process creates parts that are stronger than those manufactured by any other metalworking process. Forging takes advantage of the metal’s natural grain flow, shaping the grain flow to conform to the contours of each part’s unique geometry. This grain flow contouring is lost when cutting through the grain by machining it and is also lost when casting parts. Forging offers a single piece versus a welded unit, as the weld quality can be hard to replicate without additional inspection.
Forgings can also take nearly any shape, which reduces the need for joining multiple pieces. Reducing the joint can improve the overall strength of the unit as the forging does not need to be welded or otherwise fastened together. Some other benefits associated with forged steel, include:
- Stronger components
- Wide range of material options
- Significant cost savings
- Numerous possible shapes and sizes
- High production runs
Additionally, steel forgings allow for adherence to very close tolerances. The dies used in the forging process result in precise part dimensions with minimal part to part variation. Our offshore steel forging sources utilize dies that are custom-made to match customer specifications.
Can't Find What You're Looking For?
We're dedicated to helping and providing our customers with quality, custom metal and plastic components and fully assembled products.
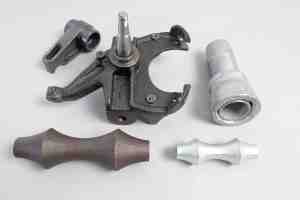
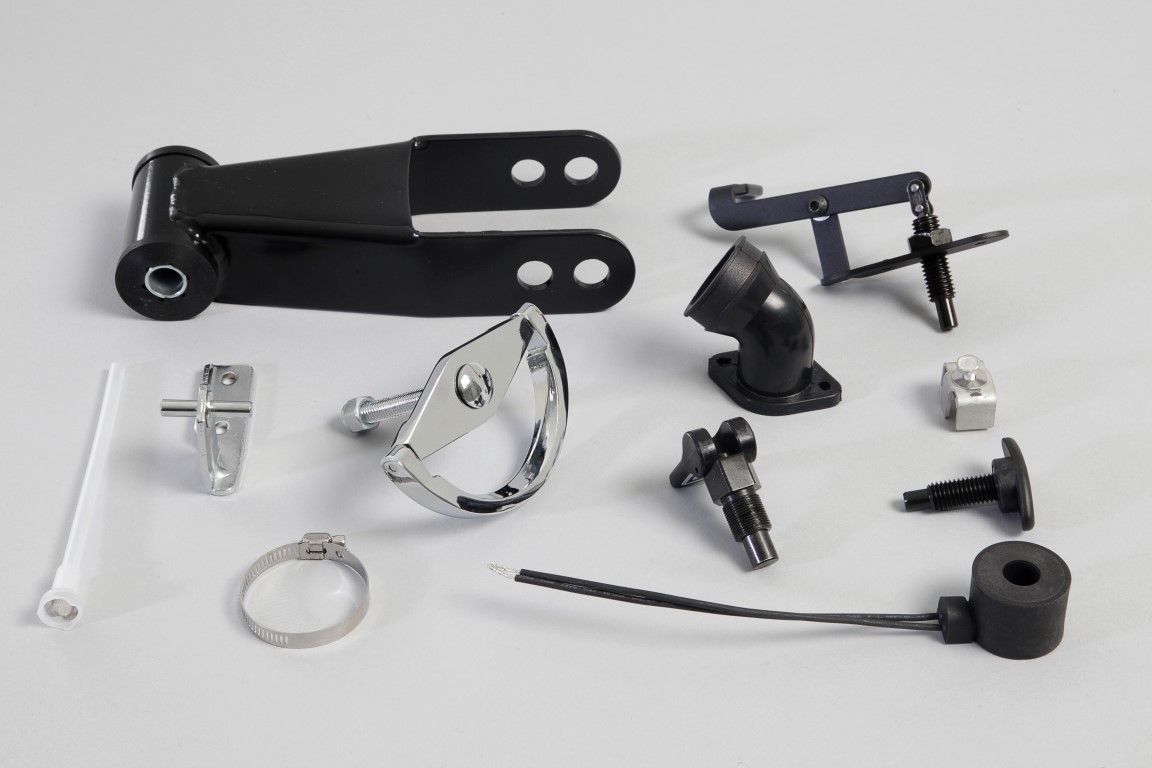
Offshore Steel Forging Advantages
Sun Fast International’s offshore sourcing provides you with an array of options for manufacturing your products. We work with the best, most reliable offshore manufacturers to ensure that your products meet or exceed your expectations for quality and precision. Some of the benefits associated with sourcing steel forging offshore include:
- Less Expensive Raw Materials - Raw materials often cost less thanks to the manufacturer’s proximity to their source. You get the same high-quality materials used domestically, but at a lower cost, due to this logistical advantage.
- Lower Labor Costs - Offshore manufacturing labor costs have historically been lower than domestic labor costs.
- Specific Equipment - Unique equipment required to manufacture your products can be prohibitively expensive, especially if it’s only needed for a brief period.
- Specialized Workers - Hiring workers who are trained to use specialized equipment, or for other production tasks, can be a challenge, as can (re)training your current staff. This is especially true if the product is intended only for limited production.
- Eliminates Operational Concerns - Staffing, equipment maintenance, and other day-to-day requirements are managed by the offshore source; some of the associated expenses will be reflected in production costs, but overall, offshore manufacturing represents a net gain and reduces operational headaches.
Forged Steel Magnetic Particle Testing
Magnetic particle testing (MT) is a non-destructive testing technique utilized to detect defects or discontinuities (such as cracks) at or near the surface in ferromagnetic metals such as iron, steel, nickel, cobalt, etc. Magnetic particle testing is primarily utilized in the industrial sector to test metal materials such as oil & gas pipelines and various metal machinery components to prevent failures or accidents. Some of the most common industries that utilize magnetic particle testing include petrochemical, automotive, and structural steel. In addition, magnetic particle testing may be utilized to inspect underwater structures such as pipelines. Since concentrated stresses can lead to further damage and failure, detecting surface and near-surface defects is critically important when dealing with forged metal products.
Forged Steel Magnetic Particle Testing Process
The first step in the magnetic particle testing process is to magnetize the object being inspected. Specialized electronic equipment is then used to magnetize the object. Ferrous iron particles (similar to metal fillings or shavings) are then applied to the object. The iron particles will be attracted to any area where the magnetic field is disrupted and will form clusters, which then reveals the defect.
Due to a visual inspection being such an important part of the testing process, there are several different types of magnetic particles that may be utilized. The choice of particles often depends upon the color or darkness of the metal being tested. The most commonly used particles include black iron particles and yellow or red iron oxide particles.
Open-Die Vs Closed-Die Forgings
There are numerous options for manufacturing forged steel by using steel forging methods. The two most common processes are closed- and open-die die forgings. While similar in the basic idea of using pressure and temperature to modify material, the two types of forging are made distinct by their use of dies to form the metal.
Open-Die Forgings
The open die forging process is also known as free forging. Through this process, the piece of metal that is deformed between the multiple dies does not completely enclose the forged steel. The dies complete the open-die forgings process by hammering and stamping the metal through a series of movements to alter its dimensions until the desired shape is achieved. Through the open-die forgings process the steel forgings are worked at temperatures ranging from 500°F to 2400°F and are eventually worked into the desired shape through hammering or pressing. Open-die forgings are often used for short-run forgings of parts that are simple, rather than complex in design, such as:
- Sleeves
- Rings
- Discs
- Cylinders
- Shafts
- Custom designs
In addition, the repeated working of the material through the deformation process increases the strength of the grain structure within the forged steel. Some additional benefits of open die forging include improved fatigue resistance and strength while also reducing voids.
Closed-Die Forgings
Closed-die forging is a forging process that is sometimes referred to as impression die forging. This process involves two or more dies that contain a precut profile of the desired component. The heated raw material is placed at the bottom of the die. The dies then move towards each other until the raw material is formed into its required shape and size.
Closed-die forging is used for applications that require high-quality components. People turn to closed die steel forgings are often utilized when a project requires strength, reliability, and resistance to fatigue. Because of this, closed-die forgings are an appealing manufacturing process for numerous industries. Some specific parts that are formed by this type of forging can be found throughout the following industries:
- Automotive
- Construction
- Defense
- Electronics
- Agriculture
- Medical
- Oil & Gas
- And more
Forging Material Grades
Our offshore forging specialists can produce durable, high strength forgings from an array of mid-range carbon steel materials. Medium carbon steel provides excellent ductility and strength and is known for its long-wearing properties. This material is popular for bolts, shafts, car axles, rails, and other parts and components that require high strength and a certain degree of flexibility. Available steel grades include, but are not limited to:
- 1035
- 1038
- 1040
- 1045
- 1050
- 1117
Several other grades of carbon steel are also available upon request. Contact us for more information regarding the materials for sourcing steel forging offshore.
Why Choose Sun Fast for Steel Forgings?
Sun Fast provides strategic sourcing for custom steel forgings manufactured to meet your exact design requirements. Our offshore forging sources produce high quality, high precision steel forgings for numerous industries, from construction to automotive and everything in between.
Sun Fast’s offshore forging sources use the highest quality steel materials available while utilizing state-of-the-art equipment to ensure superior precision and repeatability. We can deliver your forged products in fast turnaround times that fit your schedule and at prices that fit your budget.
In addition to steel forging, Sun Fast also offers offshore services for precision machining and other secondary operations to give you more complete parts and components. Contact us for more information regarding all our forged steel options, or submit a project for in-depth price analysis.